Celeritech Marketing Team | ABC Analysis and SAP Business One: A Guide to Inventory Optimization and Logistics Excellence
In the dynamic landscape of business operations, efficient inventory management is a cornerstone for success. This comprehensive guide explores the strategic importance of ABC analysis, best practices, and how incorporating tools like SAP Business One can revolutionize inventory optimization within logistics and supply chain management.
Understanding ABC Analysis in Inventory Management
ABC analysis is a sophisticated inventory management technique that categorizes items based on their importance to the business. Key factors such as demand, cost, and risk are considered to classify items into three categories: A, B, and C. This segmentation enables businesses to prioritize resource allocation for maximum efficiency and understand which products or services are most critical to the financial success of their organization.
The most important stock keeping units (SKUs), based on either sales volume or profitability, are “Class A” items, the next-most important are Class B and the least important are Class C.
The Pareto Principle says that most results come from only 20% of efforts or causes in any system. Based on Pareto’s 80/20 rule, ABC analysis identifies the 20% of goods that deliver about 80% of the value.
Therefore, most businesses have a small number of “A” items, a slightly larger group of B products and a big group of C goods, a category that that defines the majority of items.
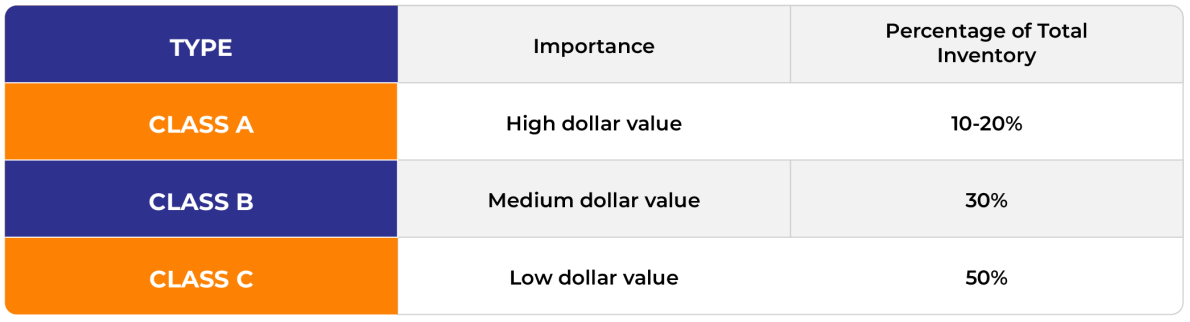
The Pareto Principle may not always be completely accurate. However, analysis shows that valuable things do tend to bend toward an 80/20 distribution. ABC analysis identifies the “sweet spot” where most of a business’s revenue comes from with relatively little effort.
How is ABC calculated?
Conduct ABC inventory analysis by multiplying the annual sales of a certain item by its cost. The results tell you which goods are high priority, and which yield a low profit, so you know where to focus human and capital resources.
Use this formula for ABC inventory analysis:
(Annual number of items sold) x (Cost per item) = (Annual usage value per product)
Benefits of ABC Analysis
ABC helps better control working capital costs. The information gained from the analysis reduces obsolete inventory and can boost the inventory turnover rate, or how often a business has to replace items after selling through them.
Simplified Inventory Managers work:
- Inventory managers are always looking for ways to improve pricing and quality or to achieve greater efficiencies. ABC technique can be applied as the “always better control” method to help them focus their time and effort primarily on Class A inventory and less on B and C class products.
Optimized Inventory Management:
- Prioritizing items based on their importance ensures focused and efficient resource allocation.
Improved Inventory Forecasting:
- Monitoring and collecting data about products that have high customer demand can increase the accuracy of sales forecasting. Managers can use this information to set inventory levels and prices to increase overall revenue for the company.
Better Pricing:
- A surge in sales for a specific item implies demand is increasing and a price increase may be reasonable, which improves profitability.
Informed Supplier Negotiations / Improved Supply Chain Efficiency:
- Since companies earn 70% to 80% of their revenue on Class A items, it makes sense to negotiate better terms with suppliers for those items. If the supplier will not agree to lower costs, try negotiating post-purchase services, down payment reductions, free shipping or other cost savings.
Streamlined Logistics Management:
- ABC analysis aids logistics professionals in identifying and managing high-priority items critical for supply chain optimization.
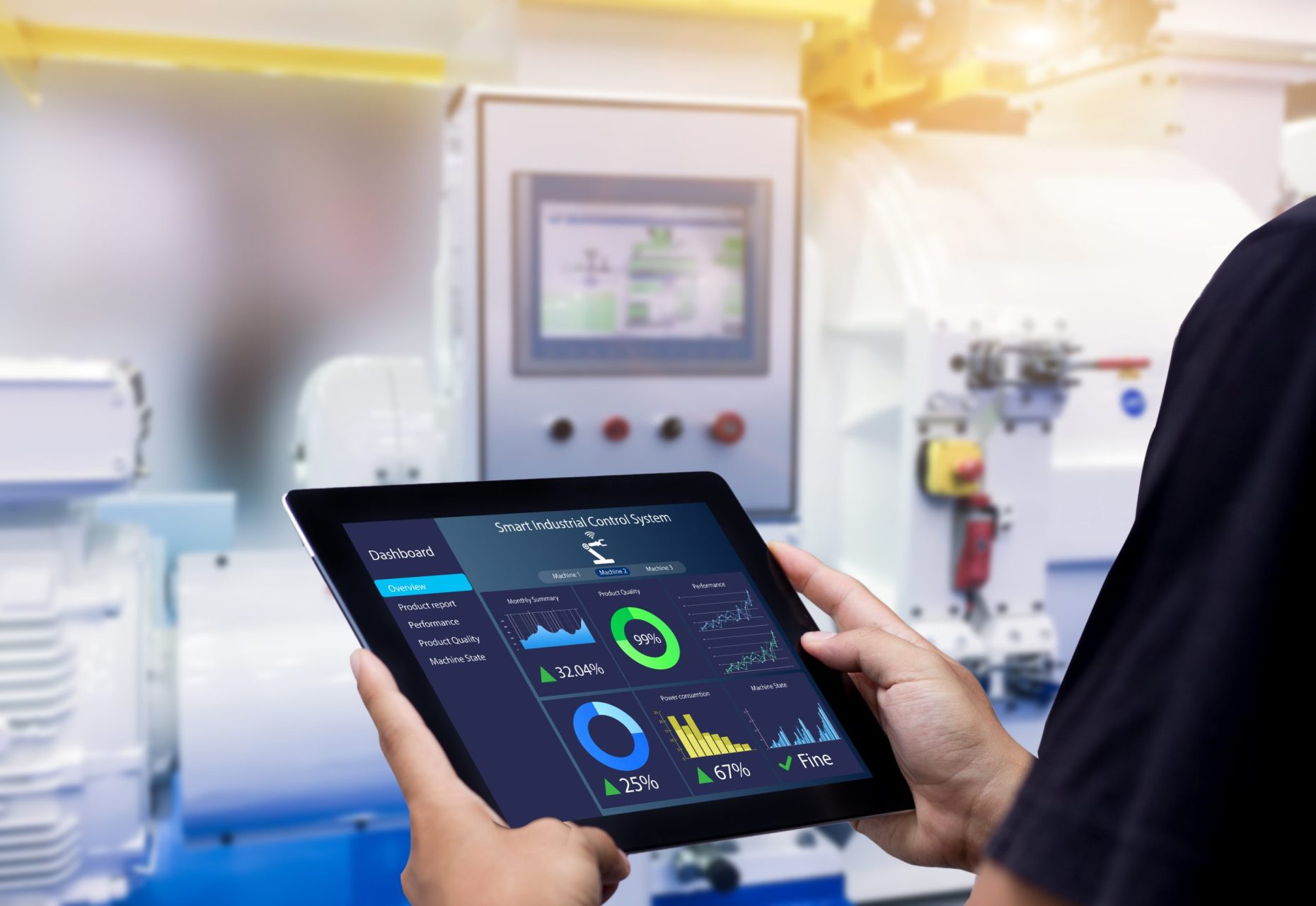
Performing ABC using SAP Business One step-by-step
To unlock the full potential of ABC analysis, businesses should adhere to the following best practices:
Identify the Objective:
An ABC analysis can help you meet one of two targets: lower procurement costs or raise cash flow by optimizing inventory levels of the right items based on customer sales or production.
Collect Data:
The most common data to collect is the annual spend on each item. This data is in raw purchase dollars. Use the Procurement Analysis Report to get the total amount invested either by item, by supplier, by buyer. If it’s easy to calculate, you can gather the weighted cost, including gross profit margin, ordering and carrying cost data.
Sort by Decreasing Order of Impact:
Use the ABC analysis formula to rank each inventory item’s order by cost — from highest to lowest impact.
Calculate the Sales Impact:
For each inventory item, calculate its impact on sales as a percentage by dividing the annual item cost by the aggregated total of all items spent. This number is the percent, or fraction, that you will use to compare items in the list.
Here’s the formula: % Impact = (annual item cost) / (aggregated total of all items spent) x 100
Sort Items into Buy Classes:
Assign classes to each product based on contract renegotiation, vendor consolidation or implementing e-procurement. Making changes in these areas can provide significant savings or ensure the in-stock availability of Class A items. Take a holistic view rather than being strict about the 80/20 rule.
Analyze Classes:
Once categories and strategic cost management are defined, schedule reviews to monitor the success or failure of decisions. Celeritech can help you updating the ABC criteria for each product based on certain criteria such as the average sales the last 6 months, 12 months, based on the inventory turn, or any other logical criteria you have.
SAP Business One’s ERP Software Helps Inventory Managers Make the Most of ABC Analysis
To simplify and automate selective control, ERP systems that include ABC analysis has become a standard tool for inventory managers. With ERP, users can execute full ABC analysis based on user-defined criteria, risk analysis and schedule optimization.
SAP Business One helps businesses:
- Maintain optimum supply levels with real-time inventory visibility that helps them avoid overstocks and stockouts.
- Provide predictive analytics to anticipate demand dips or spikes and alert inventory teams if there’s a change in demand or stock levels.
- Cycle counting provides a system of checks and balances to ensure the inventory records in the inventory management system are accurate. You can use the standard physical count into SAP to run regular cycle counting scheduled by classification, ensuring more regular cycle counting is performed on Class A items — those which make the biggest and most significant impact on sales performance — than Class B and C items.
Its features also include:
Logistics Management Excellence:
- Apply ABC analysis principles to logistics management for improved supply chain visibility and efficiency, in 2 clicks.
Warehouse Management Strategies:
- Incorporate ABC analysis into warehouse management strategies to ensure optimal space utilization and item accessibility.
Supply Chain Optimization:
- Integrate ABC analysis into supply chain optimization efforts for targeted resource allocation and improved performance.
Real-time Inventory Visibility:
- SAP Business One also provides real-time insights into inventory levels, aiding accurate ABC analysis.
Advanced Reporting and Dashboards:
- Customizable reporting and dashboards offer logistics professionals a comprehensive view of inventory performance.
Elevating Inventory Management with ABC Analysis
In conclusion, mastering ABC analysis and integrating tools like SAP Business One is paramount for businesses seeking inventory excellence. The synergy between ABC analysis and logistics, supply chain, and warehouse management fosters a holistic approach to inventory optimization.
By adopting best practices and leveraging advanced technologies, businesses can navigate the complexities of modern inventory management, ensuring sustained success in today’s competitive landscape.
If you require any support to make your ABC report within SAP works for you, please reach out to us at [email protected] and someone in our Customer Success Team will assist.